Ordeño Mecánico en la ganadería de leche
Principios básicos del ordeño mecánico
El ordeño mecánico constituye uno de los avances tecnológicos que han contribuido para alcanzar los parámetros actuales de producción en las explotaciones lecheras. Desde su concepción mecánica elemental, el ordeño mecánico trata de imitar la acción del becerro al mamar, es decir, succiona la leche provocando un diferencial de presiones, aplicando al pezón una presión negativa conocida como vacío parcial, sustituyendo la boca, tracto digestivo y pulmones por pezoneras, pulsador, bombas de vacío y una serie de elementos complementarios que permiten al ganadero extraer la leche de una manera eficiente y sanitaria.
Los conceptos de presión y vacío son manejados en forma muy usual en ordeño mecánico. Por esta razón es importante conocer su origen; nuestro planeta esta rodeado por una capa de aire llamada atmósfera. El aire posee masa y por consiguiente esta sujeto a la fuerza de la gravedad la cual se expresa como fuerza por unidad de área. Dado que el aire es un gas esta presión actúa en todas direcciones sobre la superficie de la tierra y sobre todos los cuerpos, tales como animales y seres humanos.
Por lo anterior se obtiene que presión atmosférica es la medida del peso de una columna de aire sobre una superficie horizontal determinada; debido a esto, la presión atmosférica disminuye con el aumento de altitud sobre la superficie terrestre, pues es menor el peso de aire a soportar.
La presión atmosférica a nivel del mar tiene un valor nominal de 100 kilo pascales (KPa) equivalente a 14.5 lb/pulg/2. Tanto la gente como los animales viven en condiciones ambientales de presión atmosférica, así mismo la mayor parte de la maquinaria opera en condiciones iguales, para razón de medidas prácticas la presión atmosférica es tomada como cero y sobre la base de esta escala una presión menor de la presión atmosférica es llamada vacío (presión negativa abajo de la presión atmosférica, que es considerada cero.
Tanto el movimiento del aire como el de la leche a través de un conducto se rigen por las leyes físicas del transporte de fluidos, sobre todo en el caso de las ordeñadoras mecánicas donde ambos elementos se transportan juntos y las condiciones de flujo se vuelven muy complejas para su análisis teórico. Por otra parte el correcto funcionamiento del sistema depender de que no existan fluctuaciones de vacío principalmente en la unidad ordeñadora y en el aspecto mecánico, alrededor de estos factores se ha desarrollado una buena parte de las investigaciones y cambios que en manera de diseños se han generado en las ordeñadoras los últimos 15 años.
Existen en el mundo varias normas o estándares que indican los requisitos que debe llenar un sistema de ordeño mecánico para su correcta instalación y funcionamiento, estas normas se han obtenido con la intervención y experiencia teórica, técnica y práctica en muchos hatos y durante muchos años.
Dentro de estas normas destacan las normas ISO (Suecia y parte de Europa), DIN (Alemania y parte de Europa), el Anteproyecto de Normas Mexicanas (México), y el Estándar 3-A de Estados Unidos y Canadá.
El estándar 3-A es el que reúne los fundamentos técnicos categóricos indispensables, ya que los principales investigadores del ramo concuerdan en que el diseño del sistema de ordeño mecánico sobre la base de este estándar, esta mejor adaptado a la fisiología de la vaca y a los parámetros de producción que se obtienen actualmente, dado el potencial genético y las prácticas adecuadas de manejo, sanidad y alimentación que se encuentran establecidas en las principales explotaciones. Otros factores determinantes son el hecho de que los sistemas de ordeño mecánico instalados bajo este estándar desplazan un volumen de leche mayor en el tiempo óptimo y presentan menos fluctuaciones de vacío en la unidad
de ordeño.
Los principios mecánicos en los sistemas de ordeño giran alrededor de dos puntos
particularmente significativos:
1. – La maquina de ordeño aplica vacío parcial al pezón creando una presión deferencial a través del canal de salida de este, abre el conducto del pezón, extrae la leche de la cisterna del pezón y por una tubería la vierte en un recipiente.
2. – Ejerce una acción de masaje intermitente en el pezón para facilitar la circulación de sangre y evitar la congestión en la porción distal del pezón. Un equipo de ordeño adecuadamente diseñado, instalado y bien operado logra la correcta aplicación de estos principios.
Componentes de un equipo de ordeño mecánico
Para comprender mejor en que consiste un equipo bajo estas características, se enumeran a continuación los elementos principales que la integran, así como las recomendaciones mas adecuadas de diseño en cada uno de ellos.
Bombas de vacío
Fundamentalmente la bomba de vacío extrae aire del sistema de ordeño, es decir, crea una presión negativa conocida como vacío parcial que al aplicarse al pezón de la ubre, la presión fisiológica positiva que existe en esta, empuja la leche al área de presión negativa que existe en el sistema.
El vacío generado por la bomba es utilizado en el sistema para tres funciones principales: proporcionar masaje al pezón durante la fase de descanso, provocar la salida de leche y auxiliar en la conducción de la leche a través de las tuberías. Existen básicamente tres tipos de bombas de vacío: las bombas de pistón, rotativas y las hidráulicas o centrifugas.
Bombas de pistón
Pueden ser de baja o alta velocidad, las de baja velocidad consumen poco aceite y requieren poco mantenimiento además de ser silenciosas. Las de alta velocidad, tienen una mayor capacidad de producción de vacío.
Bombas rotativas
Pueden ser de alta y baja velocidades, esta se determina por las revoluciones por minuto a que gira el motor, proporciona mayor capacidad de vacío, comparadas con las de pistón para un mismo caballaje, requieren poco mantenimiento y también son silenciosas.
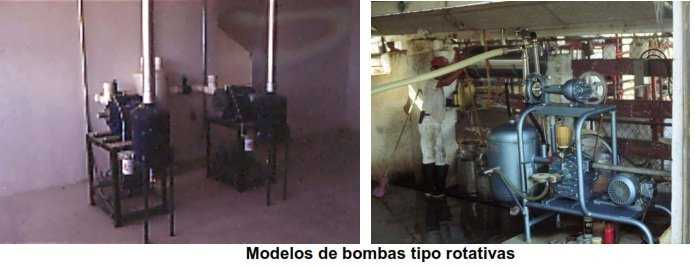
Bombas hidráulicas o centrífugas
Estas bombas no se afectan con los líquidos que llegan a ellas y proporcionan un vacío uniforme, pero requieren agua para su operación y se dañan con la presencia
de sólidos.
Las bombas rotativas son las mas generalizadas comercialmente y aunque varían en sus principios, la finalidad de las tres es crear el vacío necesario para contar con un ordeño adecuado, tomando en cuenta el número de unidades ordeñadoras en operación, la longitud, diámetro e interconexión de las tuberías del sistema y el volumen de leche desplazada, además de contar con un 50% de reserva efectiva.
La capacidad de la bomba de vacío normalmente es medida en pies cúbicos por minuto (PCM) y litros por minuto (lt/min.); es decir, la cantidad de aire que en un minuto es capaz de desplazar la bomba medida en pies cúbicos o en litros.
La bomba debe proporcionar óptimamente 8 a 10 PCM (3.7 a 4.7 lt/seg.) De acuerdo a la Asociación Americana de Ingenieros Mecánicos (ASME) por cada unidad de ordeño a 15″Hg.
Como la demanda total de vacío varía con respecto a la presión atmosférica y altura sobre el nivel del mar es necesario considerar la existencia de un factor de corrección para lograr la capacidad real de la bomba a la altura a la que esta operando
Existe de una forma práctica una ley de granja que nos indica que un caballo de fuerza (HP) en el motor de la bomba es equivalente aproximadamente a 10 PCM (ASME) de capacidad al nivel del mar, de donde resulta factible decir que se requiere 1 HP en el motor de la bomba, por cada unidad de consumo en el sistema.
La bomba de vacío debe ser aislada eléctricamente del resto del sistema para evitar pasos de corriente al salón de ordeño, lo que ocasionaría accidentes, controlando esto mediante aislantes de hule y tuberías de conducción de PVC.
La bomba de vacío debe estar protegida del polvo por un filtro y de la posible llegada de liquido a la misma, por un tanque interceptor con drenaje automático, con capacidad mínima de 15 L.
La fuente de energía para generar el vacío por la bomba es generalmente corriente eléctrica, pero también es posible emplear motores de gasolina o tomas de fuerza de un tractor.
Tanque de distribución de vacío
Su propósito es mantener una reserva de vacío para las posibles fluctuaciones, así como cerrar en el todos los ramales de abastecimiento de vacío, para evitar puntos ciegos y conexiones en “T” que incrementan las fricciones y dificultan el libre desplazamiento del aire, las cuales pueden ser causadas por:
a) Fugas al conectar o desconectar las copas.
b) Sobrecarga del sifón ordeñador.
C) Fugas de los pulsadores.
D) Exceso de conexiones y codos en el sistema.
El suministro de vacío a las líneas de pulsadores y maquinas ordeñadoras no debe presentar fluctuaciones, por lo que se recomienda que el tanque de distribución tenga una reserva de por lo menos el 50% de la capacidad de la bomba, es decir, de 18 a 20 lt. por unidad de ordeño. En instalaciones donde el número de unidades ordeñadoras sea mayor a 8, se podría emplear un tanque de 160 lt. Este tanque debe contar con drenaje automático en el fondo, estar colocado lo mas cerca posible de la trampa sanitaria y del tanque de recibo de leche y conectado a la bomba superiormente por un tubo lo suficientemente ancho para evitar pérdidas de vacío y paso de líquidos.
Las pérdidas en el tanque de distribución de vacío no deben ser mayores a 2 PCM con relación a la capacidad medida en la salida de la bomba.
Reguladores de vacío
La función del regulador de vacío es mantener el nivel de presión negativa en el sistema, siempre al valor predeterminado, evitando de esta forma que el nivel de vacío en el sistema pueda ser mas elevado de lo establecido y provoque prejuicio en la glándula mamaria, o bien restablezca con rapidez el nivel deseado evitando fluctuaciones de vacío que predispongan a mastitis a la vaca.
Este aditamento constituye la válvula reguladora que previene que el vacío del sistema sobrepase él limite preestablecido a través de permitir la entrada de aire.
Los reguladores de vacío deben tener capacidad suficiente para admitir una cantidad de aire igual a la de la capacidad de la bomba trabajando a plena carga.
Existen básicamente tres tipos de reguladores:
1) Los que funcionan a través de un mecanismo de resorte.
2) Los que funcionan con un mecanismo de contra peso.
3) Los que funcionan con un sensor remoto automático.
Debido a la disponibilidad de líneas de leche bajas, a las diferencias en la resistencia
de las pezoneras de silicona para abrirse y a la gran variación en las técnicas de ordeño, es aconsejable instalar reguladores de vacío que puedan ajustarse fácilmente para satisfacer las necesidades que se requieren en un momento dado.
Los reguladores deben ser colocados en forma de parejas, con un nivel de vacío predeterminado en el sistema que ser de 15″Hg. para equipos con línea de transporte de leche elevada y de 13 a 13.5″Hg. para sistemas de línea baja.
El vacío aplicado al pezón nunca deber exceder de 13”Hg. ; Es recomendable el uso de un regulador con capacidad de alto consumo extra, calibrado a 16 o 17″Hg. justo en el ramal de salida de la bomba de vacío, esto ser para dar protección, tanto a la bomba como a la vaca que se ordeña, en caso de emergencias ocasionadas por
fallas en los reguladores normales montados en el sistema.
Medidor de vacío
Es el aparato que mide el nivel de vacío en el sistema, esta calibrado en pulgadas de mercurio y en ocasiones en centímetros o milímetros de mercurio.
El de uso más común es el modelo de reloj, calibrado en unidades barométricas, con escala de 0 a 30 “Hg o de 0 a 760 mm de Hg. Aparte del modelo de reloj, existe el medidor de columna de mercurio calibrado en pulgadas de Hg que es más exacto y sensible que el anterior.
Un sistema de ordeño adecuado debe contar con dos medidores de vacío, uno instalado en el tanque de distribución o en el ramal de abastecimiento que va del tanque a la trampa sanitaria, y otro más en un sitio visible para el ordeñador. Es recomendable utilizar el primero de columna de mercurio y el segundo, de reloj (vacuometro)
Línea para vacío y pulsación
Es la red de conductos no sanitaria que abastece el vacío generado por la bomba al tanque de distribución, a la línea de pulsación, a los pulsadores, a los casquillos de la unidad para ordeño, a la trampa sanitaria y a la línea de ordeño y lavado, cuando el sistema funciona con jarras pesadoras. Es recomendable usar en estas líneas P.V.C. por ser aislante de la corriente eléctrica, por la facilidad de lavado y la instalación.
Una especificación técnica deseable en el sistema de ordeño mecánico, es contar con los diámetros adecuados en cada una de estas líneas.
Las líneas para vacío deben contar con declives adecuados, codos amplios, drenajes en los puntos inferiores, puntos de medición a lo largo de las líneas, grifos o tomas de vacío para los pulsadores salientes de la parte superior del tubo, con diámetros continuos sin ninguna reducción. La altura máxima de la línea al piso de la vaca no debe ser mayor a 1.80 m.
Las líneas de vacío deberán también ser lo mas rectas y cortas posibles ya que una excesiva longitud o muchas curvaturas reducen significativamente el flujo de aire.
Trampa sanitaria
El objetivo primordial de la trampa sanitaria es el de prevenir el contacto de la leche con el aire del sistema debido al movimiento de liquido de un lugar a otro. Esta trampa puede ser de vidrio, material plástico o acero inoxidable.
La trampa sanitaria es el punto de unión donde se separa el equipo en dos grandes partes, la parte que tiene contacto con la leche y la que no lo tiene.
La conexión entre el jarro final de recibo y la trampa sanitaria debe tener una pendiente hacia esta, previniendo cualquier posibilidad de que el flujo reversible de gotas minúsculas de leche con bacterias puedan contaminar el tubo.
Dicha conexión no deber medir más de 30 cm y deberá permitir su fácil limpieza.
Línea para transporte de leche
Su propósito fundamental es transportar de manera eficiente, leche y aire hasta la jarra donde se recibe la leche; en donde el aire y la leche son separados posteriormente.
Las tuberías para leche deben ser de vidrio o acero inoxidable y tener totalmente un acabado sanitario.
Las de acero inoxidable, son más durables y más económicas a largo plazo. Una de sus principales cualidades es la de poder colocarse a una altura inferior a la de la ubre, sin riesgo alguno. Deben tener suficiente diámetro par evitar sobrecargas de leche y agitación excesiva.
En la determinación del diámetro adecuado de la tubería para leche se deben considerar los siguientes puntos:
a) Tipo de tubería (final cerrado, curvatura amplia, curvatura estrecha.
b) Número de máquinas a emplear
C) Producción media de las vacas.
Una característica deseable en el sistema de ordeño mecánico, es contar con diámetros adecuados con relación al número de unidades que el equipo posee; es importante que 1/3 parte del interior de la línea este cubierta por leche durante la carga máxima de transporte y 2/3 partes por vacío.
Técnicamente también es recomendable el uso de líneas bajas, ya que estas mueven mayor volumen de leche en el mismo espacio de tiempo, benefician la estabilidad de vacío y aprovechan en mayor proporción la fuerza de gravedad para transportar la leche.
No deben existir subidas ni bajadas en la línea que ocasionen taponamientos y detengan la adecuada velocidad en el desplazamiento de la leche. Se debe contar con declives adecuados de mínimo 1% en dirección a la unidad final de recibo.
Existen cuadros en donde se muestra el diámetro de tubo recomendado de acuerdo al número de maquinas de ordeño y sistemas de tubería empleado.
El aire y la leche, provenientes de la unidad de ordeño, deberán entrar a la línea para leche por la parte superior de este tubo. Si la entrada fuera por la parte inferior, ocurrirán disturbios en el vacío cuando la leche proveniente de otras unidades pase por esa entrada. Además, la entrada por la parte superior reduce la posibilidad de la transmisión de bacterias causantes de mastitis, debido al regreso de la leche contaminada.
Jarro final de recibo y bomba para leche
El propósito fundamental es contar con un recipiente para el recibo de leche procedente de las unidades ordeñadoras y el traslado de ésta al tanque de almacenamiento, a través de una bomba sanitaria.
El jarro final de recibo debe tener la entrada de la tubería de leche en el tercio superior para asegurar la estabilidad de vacío. Debe estar localizado lo más cerca posible de la sala de ordeño, para evitar la prolongación excesiva de la tubería (incluso podrá instalarse en uno de los extremos del foso de los operadores) en la sala de ordeño. El jarro debe ser de acero inoxidable preferentemente.
El jarro final de recibo debe contar con tantas entradas como tuberías de leche existan. Este jarro esta conectado a una bomba que es accionada cuando el nivel de leche llega a un sensor colocado en el interior. Durante esta acción la bomba transporta la leche al tanque de enfriamiento. Es importante que la bomba se desconecte automáticamente cuando el jarro todavía no este vacío; esto impide que la leche se ventile excesivamente incrementando la posibilidad de enranciamiento.
Las bombas podrán ser centrifugas, helicoidales o rotatorias.
El pulsador
Cuando la copa de ordeño de la máquina se coloca en el pezón, el vacío del sistema crea una presión negativa tanto en el interior de la pezonera como en el espacio que existe entre el casquillo y esta. La presión negativa en el interior de la pezonera provoca que la copa se mantenga pegada al pezón hace que el orificio del mismo se abra y que la leche que se encuentra en el pezón y la cisterna fluya hacia afuera.
La función del pulsador es dirigir alternativamente vacío y aire al espacio entre la pezonera y el casquillo, produciendo dos fases:
a) Fase de descanso o masaje.
b) Fase de ordeño.
En la fase de descanso la diferencia de presiones entre el interior de la pezonera y la presión atmosférica en la parte externa de la misma provoca que esta se colapse apretando y dando una acción de masaje al pezón, forzando a la sangre ha circular. En la fase de ordeño el pulsador cierra la entrada de aire atmosférico, restablece la presión negativa y la pezonera regresa a su forma normal; en este momento es cuando tiene lugar la extracción de leche.
En sistemas que trabajan con pulsadores individuales para cada unidad y otros que traban con uno maestro, que funciona para dos o más unidades de ordeño simultáneamente.
La mayoría de las máquinas trabajan a una velocidad de 40 a 60 pulsaciones por minuto. Una velocidad mayor impide que se obtenga un período de descanso adecuado y que se realice el masaje necesario del pezón para mantener la óptima circulación sanguínea.
La fase de ordeño de un buen pulsador debe ocupar de 3 a 5/25 de segundo y la fase de descanso, debe mantenerse por lo menos 10/25 de segundo, a una completa presión atmosférica.
Como ya se ha mencionado el pulsador permite la entrada intermitente de vacío o aire atmosférico hacia el espacio entre el casquillo y la pezonera y que el tiempo que se requiere para un ciclo completo es de aproximadamente un segundo. El ciclo completo hace un total de 100% y la tasa de pulsación normalmente varia de 50:50 a 70:30. El primer número se refiere al porcentaje del ciclo en que el pulsador permite la entrada de vacío, abriendo la pezonera y permitiendo la salida de leche.
El segundo número indica la cantidad de tiempo en que entra aire atmosférico, colapsando la pezonera y masajeando el pezón.
Una tasa de pulsación 70:30 permite ordeñar a las vacas más rápidamente que una 50:50, es importante no sobrepasarse en estas relaciones, ya que tasas de pulsación amplias imponen un estrés al pezón que le puede causar daño, especialmente a niveles de vacío moderadamente altos (más de 14 “Hg)
Las máquinas que cuentan con sistemas de pulsación uniforme ordeñan dos cuartos mientras los otros dos están en descanso. Algunas maquinas están equipadas con sistemas más sofisticados que permiten, por ejemplo, tener diferentes tasas de pulsación para los dos cuartos anteriores 50:50 y para los posteriores 70:30.
El sistema de pulsación alterna mantiene el vacío de ordeño más estable cuando este es marginal o inadecuado; si el equipo falla se puede alterar la tasa de pulsaciones en lados opuestos, dando origen a la presentación de problemas secundarios.
En la sala de ordeño se centra en cierto modo el fundamento elemental del ordeño mecánico, dado que la pezonera es la única parte del sistema que tiene contacto físico con la vaca.
El propósito fundamental es permitir la aplicación del vacío al pezón. Esta constituida básicamente por el casquillo y la pezonera de hule; ambos componentes deben ser compatibles, por lo que la pezonera debe ajustarse a la perfección al tipo de casco.
a) Pezoneras
Existen diferentes tipos y formas de pezoneras en el mercado y pueden estar hechas de hule natural o hule sintético compuesto de una mezcla de dos o más materiales y de silicón.
Hay varios tipos de pezoneras pero en general hay que seguir las recomendaciones de los fabricantes de las máquinas, sobre cuales son las más apropiadas para el sistema.
Las pezoneras de silicona se presentan en tres diferentes formas: redonda, triangular y cuadrada. La forma triangular es la más popular y la que proporciona mejores resultados.
Una pezonera circular se cierra primero en el centro, donde se encuentra el esfínter del pezón y permite el masaje de este en dos lados; la forma triangular no se cierra directamente en el pezón y permite el masaje en tres lados. El diseño cuadrado no cierra tampoco directamente en la punta del pezón.
Ciertos estudios muestran que la silicona no es poroso tiene una superficie suave y no acumula los elementos presentes en la leche (Ca, Mg., Cl) o soluciones limpiadoras utilizadas antes y después del ordeñando la vaca (Cl, I) Existen pezoneras de calibre angosto (diámetro interior de menos de 7/8 de pulgada) que aparentemente permite ordeñar abajo del fólder anular del pezón. Las pezoneras de calibre más amplio sufren frecuentes desprendimientos del pezón que pueden producir daño a la glándula.
Otro tipo de pezoneras son las precolapsadas, las de anillo elástico y las de dos componentes, pezonera y tubo de leche unidos por un niple acoplador.
Los modelos de anillo elástico realizan un ordeño rápido y completo, reduciendo bastante el trepamiento de las pezoneras y la irritación de la glándula.
Las pezoneras precolapsadas tiene la ventaja de proporcionar un masaje artificial al pezón; las pezoneras de dos componentes tienen un orificio de inyección de aire en el niple lo que reduce considerablemente las posibilidades de un reflujo de leche.
La boca de las pezoneras debe ser flexible, y a medida que el diámetro sea menor la flexibilidad debe ser mayor, para permitir la perfecta expansión del pezón y que fluya adecuadamente la leche.
Hay algunos aspectos a buscar en una buena pezonera y estos son: que esta cierre completamente y se acople al pezón como un guante en el momento de descanso, que su resistencia a la acción del vacío no sea superior a 3.5″Hg. y que sea de baja porosidad, para evitar acumulación de grasa, piedra de leche y bacterias.
b) Copas metálicas o casquillos:
El tamaño de la copa debe ser específico al de la pezonera para lograr un ordeño adecuado y su longitud debe ser suficiente para permitir el correcto funcionamiento de la pezonera. esta no deber apretar a la pezonera a tal grado que se dificulte el desplazamiento del aire.
Se requiere que la luz de la pezonera a la entrada del colector ordeñador sea lo suficientemente amplia para el movimiento rápido de la leche.
c) Colector o sifón:
El colector es parte fundamental del sistema de ordeño mecánico, une a las cuatro pezoneras y recolecta la leche para transportarla de su salida a través de una manguera a la jarra pesadora o al lactoducto. Este colector debe tener diseño y capacidad adecuada (228 g mínimo), ventilación que rompa las columnas de leche y provoque cierto grado de turbulencia que empuje la leche (0.8 mm) Debe cortar vacío cuando este en posición vertical y tener un peso individual adecuado al peso total de toda la unidad de ordeño.
d) Manguera de leche y de aire:
Estas pueden estar hechas de hule o de plástico transparente, el hule tiene más flexibilidad y más larga duración, pero el plástico es más conveniente por la visibilidad aun cuando tienden a cuartearse en los extremos. Estas mangueras deben ser del diámetro propuesto por los fabricantes de la máquina una manguera de diámetro mayor puede ser más apropiada para sistemas con líneas para leche bajas.
SISTEMA DE PESADO
Una importante función del sistema de ordeño mecánico es el permitir el pesado individual de producción de las vacas para realizar una adecuada lotificación.
Existen sistemas con jarras pesadoras de cristal, con pesadores de flujo constante y pesadores proporcionales.
El sistema de jarras pesadoras, es aquel en que la producción individual de cada vaca se deposita en un recipiente de cristal refractario calibrado en libras y kilogramos.
El sistema con pesadores de flujo constante es aquel en que la producción individual de la vaca pasa a través del pesador, midiendo la producción de acuerdo al flujo de la leche.
El sistema de pesador proporcional consiste en que la producción de la vaca pasa por el pesador y solamente una parte proporcional es depositada en el recipiente calibrado a escala del cual se obtiene la lectura.
Tanques de almacenamiento y refrigeración de leche
Su propósito fundamental es almacenar y refrigerar la leche de tres ordeños de las vaca, en el caso de despacho diario o de 5 ordeños en despachos cada dos días. Deben ser de acero inoxidable, de preferencia con formas cilíndricas y rectangulares, aceptándose las elípticas y los semicilíndricos.
Existen dos tipos de tanque, los de expansión directa, en los cuales la leche se enfría en el tanque y los tanques termo que reciben la leche ya enfriada por placas a través de un banco de hielo.
Los tanques deben ser capaces de enfriar la leche bajo la siguiente secuencia: un tanque para recolección diaria debe enfriar al 50% del volumen, de 32.2 C a 10 C en una hora, con el sistema de enfriamiento funcionando durante la operación de llenado; posteriormente el sistema enfriador debe enfriar la leche de 10 C a 4.4 C dentro de la hora siguiente.
Como única diferencia, un tanque diseñado para recolección de más de un día debe enfriar el 25% del volumen y seguir el mismo proceso de enfriado. La temperatura de leche dentro del tanque no deber rebasar los 10 grados C durante la adición de leche de otros ordeños.
Evaluación del funcionamiento del equipo de ordeño mecánico y su relación con la presentación de mastitis. El correcto funcionamiento mecánico del equipo de ordeño, tiene una importancia de primer orden, debido a las repercusiones que un mal funcionamiento del mismo provoca en la glándula mamaria.
Por lo tanto es necesario realizar un chequeo general al equipo por lo menos cada seis meses, además de ser rutinario en el mantenimiento. También es importante verificar la adecuada instalación del sistema y asegurarse de que reúna las características necesarias para un buen funcionamiento.
Para realizar el chequeo del equipo de ordeño es necesario contar con herramientas especiales que permitan hacerlo:
• cinta de medir
• nivel de albañil
• vernier
• cronómetro
• equipo registrador doble de vacío
• medidor de flujo de aire
• extensión eléctrica
• tacómetro
• vacuometro
• voltamperímetro
El uso de la cinta de medir es para obtener longitudes y alturas determinadas; el nivel para verificar los declives; el vernier para medir diámetros de mangueras, pezoneras y tuberías; el cronómetro para verificar pulsaciones por minuto; el tacómetro para obtener el número de revoluciones por minuto que generan las bombas de vacío y el voltamperímetro para calcular los niveles de intensidad de la energía eléctrica.
Para conocer el número de pies cúbicos por minuto (PCM) que succiona la bomba de vacío, se utiliza el medidor de flujo de aire, el cual consta de un manómetro, de un cilindro con orificios perfectamente calibrados y un cincho con el cual se pueden ir sellando los orificios evitando el paso del aire. El flujometro se conecta a la entrada de la bomba se va girando el cilindro que sella los orificios hasta lograr que la aguja del manómetro llegue a 15”Hg. después se desconecta el motor y se retira el flujometro, para hacer la lectura de los orificios que quedaron sin tapar y que indican el número de PCM que succiona la bomba. Los orificios más pequeños permiten 1 PCM en el sistema, los orificios más grandes 10 PCM.
El registrador de vacío, gráfica los resultados de los niveles de vacío a que trabaja el pulsador, la característica de la onda de aire pulsado, cantidad de vacío en el interior de la pezonera, estabilidad de este y las alteraciones ocurridas durante el tiempo de diagnóstico.
El registrador cuenta con dos medidores para vacío calibrados en pulgadas, uno es para señalar el nivel de vacío en los tubos cortos para aire y el otro para medir la cantidad de vacío en el interior de la pezonera. También es utilizado para medir el funcionamiento del pulsador alternante, cuando se conectan ambas terminales a las pezoneras en posición cruzada y para registrar simultáneamente el nivel de vacío en el interior de la pezonera y el de la línea para el transporte de leche.
El registrador cuenta con dos velocidades, la rápida se emplea para lograr las características del aire pulsado y la lenta para monitorear ordeñando la vaca. Para realizar un análisis del equipo de ordeño es recomendable hacerlo de una manera sistemática, empezando por la bomba de vacío y terminando con la unidad de ordeño.
Existen varios cuestionarios con una secuencia lógica con relación al funcionamiento del equipo que pueden ser utilizados durante la evaluación minuciosa del mismo.
A continuación se enlistan algunas características de funcionamiento recomendables para el buen estado de un equipo de ordeño:
1. Capacidad para remover aire: de 10 a 12 PCM (Estándar Americano) a cada unidad de ordeño.
2. El vacío de ordeño a nivel de línea deber tener una presión de 15″Hg.
3. El vacío de ordeño aplicado al pezón en sistemas de cubeta debe ser de 9 a
10″Hg. Si el sistema es con línea para transporte de leche de 12 a 13″Hg.
4. Número de pulsaciones por minuto de 45 a 60.
5. Relación ordeña descanso 50:50, 60:40, 70:30.
6. Recuperación de vacío posterior a una pérdida del mismo por 5 seg. , de no más de 2 seg.
7. Fluctuaciones en el vacío de ordeño en la pezonera no mayores a 2″Hg.
8. Existir una presión de vacío para dar masaje al pezón mayor de 6″Hg.
9. Las pérdidas en el vacío suministrado por las bombas no excedan del 15% en la trampa sanitaria, del 10% en el jarro receptor de leche, de 8% en la tubería del pulsador y del 30% en todo el sistema.
10. El tanque de distribución tenga una capacidad de 9.5 litros por unidad de ordeño
o un máximo de 150 litros.
11. El número de ordeños por pezonera no exceda de 1500 – 2000 ordeños si son de una pieza y de 600 – 800 si son de anillo estrecho.
12. Las condiciones de los tubos de aire, de leche y de las pezoneras sean muy buenas.
13. La máquina ordeñadora puede intervenir en la producción de mastitis sirviendo
como vector del patógeno, lesionando la ubre pudiendo causar edema en la ubre y permitiendo la implantación de gérmenes.
El equipo de ordeño posiblemente sea la causa de que los microorganismos comiencen a introducirse a través de la punta del pezón y hacia el canal del pezón.
El equipo de ordeño puede ser el principal factor de predisposición de la ubre a nuevas infecciones, como las infecciones cruzadas de un cuarto infectado a uno no infectado en la misma vaca o bien una infección transmitida de una vaca a otra. Las causas de la mastitis son muchas y variadas, y si bien existen diferencias de opinión en cuanto a cual es el factor más importante, generalmente se acepta que el manejo durante el ordeño y el equipo de ordeño son dos de los principales. Aún cuando la mastitis clínica es más frecuente en vacas ordeñadas a mano y la subclínica es tres veces más común en las ordeñas mecánicas.
Es necesario considerar que las máquinas de ordeño pueden causar mastitis por exceso de vacío, número de pulsaciones inadecuado, fluctuaciones de vacío, tubos de vacío angostos y accesorios de hule en mal estado, entre otros.
Existen situaciones que nos hacen pensar que el equipo esta funcionando mal, ya sea por desgaste, mala instalación o exceso de uso sin una revisión y mantenimiento adecuados, así como por ser mal operado:
• Las pezoneras se caen con frecuencia.
• Existen inundaciones en la tubería de línea de transporte de leche.
• El ordeño es muy lento.
• El tiempo de recuperación es mayor al establecido.
• Incomodidad manifiesta del animal.
• Partes bajas del pezón inflamadas y congestionadas.
• Inversión o erosión del pezón.
• Formación de un anillo en la base del pezón que indica trepado de la ordeñadora.
• Un número excesivo de leucocitos en el tanque de leche detectado por la prueba
de Wisconsin o California para mastitis.
• Altos niveles de infección especialmente en animales jóvenes.
• Situaciones que nos indican que:
• Los pulsadores están funcionando mal. Un pulsador funciona mal cuando esta sucio o muy usado, esto provoca que su funcionamiento no permita uniformidad durante el ordeño, repercutiendo en la función que la pezonera tiene sobre el
pezón.
• Las bombas de vacío tienen una menor capacidad, siendo esta una de las condiciones mas frecuentes de los equipos de ordeño.
• Los reguladores de vacío son muy pequeños o se encuentran pegados.
• Los diámetros de las líneas de vacío son reducidos o interferidos provocando restricciones de vacío. Líneas de diámetro reducido y muchas uniones pueden reducir la cantidad de aire que la bomba puede remover. En las líneas de vacío pueden existir tapones de sólidos de leche, suciedad, polvo, pelo entre otros.
• La instalación y disposición inadecuadas de los lactoductos provoca una capacidad insuficiente para el transporte de la leche.
ACTIVIDADES DESARROLLADAS DURANTE EL ORDEÑO MECÁNICO
• Contar con una buena lotificación de corrales, iniciar el ordeño con las vacas altas productoras seguidas de las medianas y bajas productoras y ordeñar por último a vacas recién paridas y a las vacas con problemas de mastitis
• Ordeñar siempre a la misma hora, con diferencia de 12 horas entre mañana y tarde y de 8 horas si se ha optado por tres ordeños diarios.
• Esquilar al ganado cíclicamente de las ubres, flancos y cola.
• Supervisar que el ordeñador mantenga las uñas cortas y limpias, porte completo su uniforme además de asearse antes y durante el ordeño.
• Verificar el nivel de aceite de las bombas de vacío y que el sistema funcione adecuadamente. Hay bombas que cuentan con sistemas de recuperación de aceite, el cual es necesario cambiar cuando este demasiado quemado, lavando el recipiente con un trapo húmedo en diesel.
• Verificar la tensión de las bandas de la bomba de vacío.
• Encender los calentadores a una hora oportuna, para tener agua caliente al inicio del ordeño. Los calentadores deben ser de la capacidad adecuada al volumen de agua a emplear. Considerando que se requiere agua tibia a 40 C para el lavado de las ubres, agua a 85 C para el lavado de las pezoneras entre vaca y vaca y a 60 C para el lavado del equipo al finalizar el ordeño.
• Verificar que el orificio de inyección de aire del colector, la pezonera y el niple de unión no se encuentre tapado.
• Revisar la integridad de las pezoneras y de los tubos para leche y aire.
• Encender la bomba de vacío 15 minutos antes de iniciar el ordeño para que desarrolle toda su capacidad.
• Medir que el número de pulsaciones por minuto sea el adecuado de acuerdo a las especificaciones del equipo.
• Preparar las soluciones desinfectantes y los utensilios necesarios a utilizar.
• Arrear al ganado sin gritos, ni golpes y procurar un ambiente de tranquilidad en la sala de ordeño.
• Realizar el secado de la ubre y los pezones con toallas desechables.
• Realizar un despunte cuidadoso en una taza de fondo negro, depositando los tres primeros chorros de leche, observando las características de la misma.
• Colocar la unidad de ordeño empezando por la pezonera más lejana, evitando que estas toquen el piso o jaulas.
• Vigilar que no se presenten fugas de vacío por mal acoplamiento de las pezoneras a los los pezones durante el ordeño.
• Vigilar el flujo de leche y retirar la unidad en el momento preciso de terminado el ordeño, evitando el sobreordeño.
• Cortar el vacío y retirar la unidad de una forma suave y sin tirones.
• Sumergir las pezoneras de dos en dos en una cubeta con agua limpia.
• Lavar las pezoneras por 5 seg. con agua caliente y después sé escurrir la mquina.
• Desinfectar de medio a tres cuartos de pezón con una solución especial (sellador)
• Cambiar el agua de la cubeta de enjuague cada 25 vacas aproximadamente.
• Pesar la producción individual de leche cuando menos cada mes para poder lotificar al ganado.
LAVADO Y DESINFECCIÓN DEL EQUIPO PARA ORDEÑO MECÁNICO
La solución de limpieza que se utiliza en el lavado del sistema de ordeño mecánico esta constituida en un 99.75% por agua, por lo tanto se debe conocer el tipo de agua que existe en cada unidad de producción lechera, pues las características del agua varían de un lugar a otro.
Los diferentes componentes que el agua puede poseer forman sales conocidas como las causantes de influir en la dureza del agua.
El agua se puede clasificar, de acuerdo a la cantidad de sales presentes en ella, en:
• Agua suave
• Agua algo dura
• Agua dura
• Agua muy dura
La dureza del agua se expresa en partes por millón (ppm) de carbonato de calcio:
CaCO3.
Clasificación de la dureza del agua
Tipo de Agua ppm
Suave < 61
Algo Dura 61 – 120
Dura 121 – 180
Muy Dura > 180
Funciones de la limpieza
Ablandamiento del agua.- Esto previene que la dureza del agua interfiera con los ingredientes activos del detergente y en la formación de sales insolubles.
Saponificación.- Esto es una conversión química de desechos de ácidos grasos en jabonaduras solubles.
Emulsificación (liquido / liquido.- Esto es el rompimiento de grasas y aceites en una suspensión coloidal muy pequeña.
Dispersión (sólido / liquido) Esto es, el rompimiento de los agregados sólidos de la proteína en pequeñas partículas coloidales.
Peptización.- Esta es estrictamente una acción química que espontáneamente dispersa la proteína en la solución.
Solubilización.- Esto es estrictamente una reacción física y química.
Suspensión.- Esto sucede cuando las partículas en cuestión son suspendidas en la fase líquida.
Humidificación y penetración.- Es el resultado de reducir la tensión superficial y la tensión interfacial lo cual contribuye a humedecer y penetrar en las proteínas.
Enjuague.- Esto significa que las superficies enjuagadas sean realmente dejadas libres de las partículas problemas y del resto del detergente.
Factores que afectan la calidad de la limpieza
Cantidad de restos de leche dejados en línea de leche.- La cantidad y calidad de estos restos influencian muy significativamente en la eficacia de la limpieza. El esquema anterior demuestra la importancia de un buen enjuague antes de iniciar
el lavado del sistema.
La naturaleza y calidad de los restos de leche deben de considerarse juntas. Una vez secos, son más difíciles de ser eliminados, por lo tanto, es necesario dar un enjuague inmediatamente después de que el ordeño ha finalizado; mientras mejor sea realizado el enjuague, mejor serán eliminados los restos de leche y el proceso de limpieza ser facilitado.
La calidad y naturaleza de la superficie.- La superficie que se va a limpiar es de suma importancia dado que afecta la eficacia de dicha limpieza.
Considerando que el cristal es la superficie más fácil de limpiar, lo comparamos con otras superficies para propósitos de limpieza:
* Cristal 100%
* A. Inoxidable 80%
* Aluminio 70%
* Hule 30%
* Plástico 20%
Requerimientos para realizar un buen lavado:
Para sistemas con “Lavado en Sitio” (CIP), se debe observar que se cumplan los siguientes requerimientos:
Temperatura.– La temperatura es un factor muy importante pues depende de ella la reducción de la tensión superficial, la rapidez con que se realiza la saponificación e hidrolización y licuado de los aceites, ácidos grasos y grasa.
Concentración.– El uso de altas concentraciones de detergentes generalmente aumenta la eficacia de la limpieza, pero hasta cierto límite. Sin embargo, las concentraciones demasiado altas no mejoran de efecto y, en cambio, pueden provocar resultados inferiores. La concentración de un detergente se determina basándose en la dureza del agua, la temperatura de la solución de limpieza, el tipo de residuos de la leche y el tiempo que se le da al lavado en sí.
Acción mecánica.- Este es un factor muy importante en el proceso de limpieza,debe de permitir que la solución de limpieza activa esté en constante contacto con las superficies y los residuos a limpiar y también debe crear la suficiente acción mecánica para remover físicamente los residuos de la leche en las superficies internas. La velocidad mínima de las soluciones de limpieza debe de ser de 1.5 m/seg. ; por ejemplo, en una línea de 1.5″ de diámetro interno, se debe recuperar un volumen liquido de 45 litros en un máximo de 22 segundos.
Duración de la limpieza.- El tiempo que tome la limpieza depender de los químicos utilizados. Todas las acciones físicas o químicas de limpieza necesitan, para llevarse a cabo correctamente, un cierto tiempo. No existe ningún producto “milagroso” que sea capaz de limpiar o sanear el sistema instantáneamente. El tiempo recomendado de limpieza varía de 5 a 20 minutos.
Volumen.- Es de suma importancia que se utilicen la cantidad de agua exacta, dadoque si sobra, puede sobresaturarse el sistema, y si falta, no se logra que llegue la solución detergente a todas las áreas a limpiar durante cada ciclo de lavado.
Drenaje.- Todas las partes de que consta el sistema de ordeño por el cual se transporta leche, deben tener una pendiente adecuada para que, una vez terminado el lavado y sanitización del mismo, el sistema pueda drenar con facilidad por si mismo los restos de las soluciones utilizadas, evitando así que acumulen éstos líquidos entre ordeño y ordeño. Los drenes deben permitir la salida fácil y autónoma de estos líquidos, una vez que la acción del vacío cese por completo.
Todos los equipos deben de ser lavados total e inmediatamente después de terminado cada ordeño, y los tanques fríos también deben ser lavados en cuanto se entrega la leche.
Si el equipo solamente es enjuagado momentáneamente con agua corriente para ser lavado después, se contaminará con bacterias termofílicas (que no crecen a temperaturas de refrigeración, 4 C, pero que si en cambio sobreviven a las temperaturas de pasteurización, 62.8 C por 30 minutos) las cuales originar n problemas de calidad en la leche.
Procedimiento de lavado de la línea de leche (pasos básicos)
Enjuague prelavado.– Se debe enjuagar la línea del transporte de leche tan pronto como el ordeño haya terminado. Para ello, se debe utilizar una gran cantidad de agua tibia (35-40 C); Este prelavado debe descargarse continuamente hasta que el agua salga totalmente clara, es decir, ya sin residuos notorios de leche. Habrá que tener mucho cuidado de no sobrepasar los 45 C, pues de lo contrario se pueden
“cocer” los residuos de la leche en la superficie interior de las tuberías y ser más difícil su remoción y limpieza dado que se pegan en su interior. El agua tibia remueve mejor los residuos de la leche que el agua fría. Debemos cuidar de no reciclar esta agua del enjuague, para no dar entrada al sistema de ordeño nuevamente a los residuos de la leche. Es muy recomendable que durante todo el proceso de lavado el sistema de pulsación se encuentre funcionando, es decir, que las pezoneras estén abriendo y cerrando en su ciclo normal.
Ciclo de lavado alcalino.– Una solución alcalina clorinada que llegue a la línea de leche, al inicio, a una temperatura de 71.1 C, el cloro le ayudar a remover los residuos y disuelve las proteínas en sus elementos básicos, mientras que la alta alcalinidad (el pH >10) emulsifica las grasas. Es muy importante que la temperatura sea menor a 42 C ya que si esto sucede se van a incrustar las grasas y proteínas de la leche, en las superficies de la línea de leche. Se debe detener este lavado alcalino cuando la temperatura de la solución llegue a los 42 C y desechar la solución. La dosificación utilizada es la que el fabricante de los detergentes recomiende. Asegúrese de utilizar las cantidades exactas, tanto en el volumen del agua requerido por cada sistema, como en la cantidad de detergente alcalino en uso.
Lavado ácido.- Se debe lavar la línea dos o tres veces por semana, dependiendo ello de las condiciones del sistema, dureza del agua, temperatura en uso, etc.; para ello se debe utilizar suficiente agua tibia (35 – 45 C) a un pH de 4.0 a 4.5.
Drenaje.– Después del lavado anterior se debe permitir drenar el sistema completamente. Inspeccionar la línea y todas las partes integrales de ella, tales comolas trampas sanitarias, uniones, codos, empaques, jarras pesadoras, jarrones de recibo, etc.; y verificar que no queden inundaciones o encharcamientos interiores, es decir, que el declive sea libre y total para evitar tales acumulaciones de líquidos una vez terminado el lavado del sistema.
Es necesario desarmar rutinariamente las áreas a las cuales es posible que no alcance con la suficiente fuerza la solución limpiadora, tales como son codos, uniones, juntas, interior de colectores, etc.; por tal motivo, habrá que limpiar a mano esos pequeños puntos en los cuáles se da inicio a la acumulación de residuos y que son de alto riesgo de contaminación bacteriana. Si es el caso podría pensarse en la instalación de un inyector de aire al sistema de lavado con lo cual se le da mayor fuerza al lavado dado que da ciclos de una turbulencia extra, logrando así que la solución penetre con mayor fuerza a todas esas áreas de difícil acceso.
Higiene y desinfección.- Inmediatamente antes del siguiente ordeño, el equipo debe ser desinfectado. El producto mas comúnmente utilizado es el Hipoclorito de Sodio liquido, aunque el Cloro en polvo (Hipoclorito de Calcio) o el Iodo también se pueden utilizar. El Cloro en polvo (también conocido como HTH) es más estable; a diferencia del Hipoclorito de Sodio liquido que pierde concentración a temperaturas superiores a los 20 C y en presencia de la luz solar. El Cloro en polvo mantiene su concentración si se mantiene cubierto y seco. Se recomienda dar un enjuague con una solución final de 200 ppm de Hipoclorito de Sodio o una solución final de Iodo a 25 ppm.
El apéndice F de la “Pasteuriced Milk Ordinance” (PMO) de los E.U.A. dice lo siguiente: “Un período de exposición de un minuto de 50 ppm de Cloro debe ser mantenido cuando se utiliza una temperatura mínima de 24 C. Se considera suficiente un minuto de contacto para todos los hipocloritos, incluyendo aquellos de acción más lenta de compuestos alcalinos. Las soluciones a menores temperaturas tendrán una acción bactericida más lenta. Por cada grado centígrado menos de temperatura de la solución se necesita aproximadamente el doble de tiempo de contacto para activar la acción bactericida equivalente con la misma concentración de la solución. También se puede compensar la baja temperatura aumentando la concentración del bactericida”.
Se recomienda que los compuestos yodados no se utilicen a concentraciones menores a 12.5 ppm y que tampoco se utilicen a temperaturas mayores a 49 C dado que el Iodo se volatiliza a temperaturas altas, dando como resultado una reducción en el poder de la solución. Se debe permitir que el sistema se drene antes de iniciar el ordeño para evitar que los residuos del sanitizante se mezclen con la leche.
Los residuos de la leche consisten en grasa, proteína, carbohidratos y sales minerales (incrustaciones y fosfatos).
Tradicionalmente se considera que:
• Los productos cáusticos remueven la proteína, la grasa y los carbohidratos.
• Los productos ácidos remueven la piedra de leche, incrustaciones y restos de la dureza del agua.
• La grasa es insoluble en ácidos, agua y álcalis.
La grasa debe ser removida por la interacción entre la temperatura, la acción de la fuerza mecánica, y la emulsificación realizada por los agentes surfactantes.
Los carbohidratos generalmente son solubilizados bien en soluciones acuosas.
Los restos de los carbohidratos pueden necesitar la ayuda de oxidantes.
La piedra de leche esta constituida por carbonatos y fosfatos de Calcio.
Los residuos costrosos están constituidos por carbonatos de Calcio y Fosfatos de Calcio. Estos están presentes en las costras que se observan y su remoción depende de las temperaturas del lavado con los productos de la limpieza.
Propiedades del Hidróxido de Sodio y de Potasio:
Ventajas:
* Buena emulsificación.
* Rápida solubilidad.
* Buena saponificación.
* Buena floculación.
* Buena actividad germicida.
Desventajas:
* Se precipita con el agua.
* Es corrosivo.
* Difícil de enjuagar.
* Requiere de manejo cuidadoso.
Propiedades de los Fosfatos:
Ventajas:
* Buen secuestrante.
* Alto grado de amortiguación.
* Buena floculación.
* De fácil enjuague
Desventajas:
* Alto costo.
* Baja calidad de limpieza.
* Insoluble.
* Cambia a ortofosfatos.
* Corta vida media.
Propiedades de los ácidos:
Ventajas:
* Remueven los depósitos cálcicos.
* Neutralizan los residuos alcalinos.
* Remueven las costras de la dureza del agua.
* Disuelven las sales minerales.
* Proveen el enjuague ácido.
* Conservan las superficies brillantes.
* Favorecen la limpieza.
Desventajas:
* Corrosivos.
* Producen gases tóxicos.
* Son de difícil manejo.
* Son de fácil reacción.
* Funciones de un detergente efectivo:
* Rápida penetración y alto poder humectante.
* Habilidad en el control de agua dura.
* Alto grado detergente.
* Fácil enjuague.
* No corrosivo.
No existe ningún químico (alcalino, agente humectante, etc.) que pueda suplir todas las propiedades anteriormente mencionadas y que pueda proveer una limpieza efectiva por sí solo.
Excelente articulo
MAGNIFICO ARTÍCULO, CONTIENE MUCHA INFORMACIÓN SUMAMENTE INTERESANTE
Muchas gracias colega
Muy buen articulo me sirvio para mi tarea
Muy buena información ya que estoy empezando con mi producción de leche
Excelente artículo
EXCELENTE ARTICULO, UNA EXPLICACIÓN MUY AMPLIA Y COMPLETA, EN TODOS LOS PROCESOS DEL ORDEÑO.
Una revisión sencilla y completa del ordeño mecánico. Muchas gracias